It’s all in the coating – creating longer lasting steel products
It’s all in the coating – creating longer lasting steel products
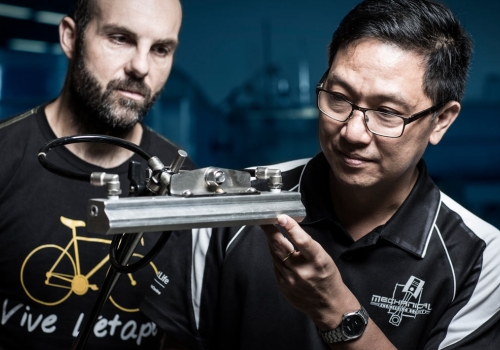
BlueScope, a provider of innovative steel materials, products, building systems and one of the world’s leading manufacturers of painted and coated steel products, is drawing on expertise at the ARC Research Hub for Australian Steel Manufacturing (Steel Research Hub), administered by the University of Wollongong (UOW) to investigate complex manufacturing challenges for creating more durable building products.
One of the critical challenges being addressed by a joint UOW-BlueScope-University of Queensland research team at the Hub is how to produce smooth, uniform, thin metallic alloy coatings on high-quality coated steel products.
Coated steel products – such as corrosion-resistant metallic alloy coated steels – are important for Australian steel manufacturers, particularly in building applications that must withstand the demands of the harsh Australian climate for extended periods.
Associate Professor Buyung Kosasih, a Chief Investigator with the Steel Research Hub, says that the research team has developed mathematical and numerical models that help to predict the coating process under different operating conditions.
Metallic alloy coatings are applied to a strip of steel by first passing the strip through a molten alloy bath, such as in hot-dip galvanising; then, as the strip passes out of the bath, an air jet knife is used to blow or ‘wipe’ away the excess coating material to achieve the desired coating thickness and uniformity. A uniform coating is a more durable finish, less likely to corrode.
The Steel Research Hub has made a measurable impact on maintaining an advanced, competitive steel manufacturing industry in Australia, one that is able to provide high quality, locally produced steel for customers in residential construction, defence, infrastructure and transportation systems. |
BlueScope, a provider of innovative steel materials, products, building systems and one of the world’s leading manufacturers of painted and coated steel products, is drawing on expertise at the ARC Research Hub for Australian Steel Manufacturing (Steel Research Hub), administered by the University of Wollongong (UOW) to investigate complex manufacturing challenges for creating more durable building products.
One of the critical challenges being addressed by a joint UOW-BlueScope-University of Queensland research team at the Hub is how to produce smooth, uniform, thin metallic alloy coatings on high-quality coated steel products.
Coated steel products – such as corrosion-resistant metallic alloy coated steels – are important for Australian steel manufacturers, particularly in building applications that must withstand the demands of the harsh Australian climate for extended periods.
Associate Professor Buyung Kosasih, a Chief Investigator with the Steel Research Hub, says that the research team has developed mathematical and numerical models that help to predict the coating process under different operating conditions.
Metallic alloy coatings are applied to a strip of steel by first passing the strip through a molten alloy bath, such as in hot-dip galvanising; then, as the strip passes out of the bath, an air jet knife is used to blow or ‘wipe’ away the excess coating material to achieve the desired coating thickness and uniformity. A uniform coating is a more durable finish, less likely to corrode.
Associate Professor Buyung Kosasih says that their mathematical model is the first that links instability of the air jet knife to potential non-uniformities in the coating surface. This has highlighted a critical operating threshold that produces either a smooth or a rough coating finish of the metallic alloy coating. The team has now employed laboratory-scale experiments carried out at BlueScope facilities to assist in the selection of air jet knife operational and design settings in industry.
The Steel Research Hub originally launched in 2015, with a second successful Hub awarded $5 million from the ARC in 2020, securing a further $23.4 million cash and in-kind from collaborating industry and other university partners.
Associate Professor Buyung Kosasih says that their mathematical model is the first that links instability of the air jet knife to potential non-uniformities in the coating surface. This has highlighted a critical operating threshold that produces either a smooth or a rough coating finish of the metallic alloy coating. The team has now employed laboratory-scale experiments carried out at BlueScope facilities to assist in the selection of air jet knife operational and design settings in industry.
The Steel Research Hub originally launched in 2015, with a second successful Hub awarded $5 million from the ARC in 2020, securing a further $23.4 million cash and in-kind from collaborating industry and other university partners.